Introduction
The HybSi® membrane can separate liquid mixtures more efficient than e.g. distillation by using a pervaporation process. On this page, you will get an answer to the following questions:
- What is pervaporation exactly?
- What makes this technology much more sustainable that other separation processes?
- Why is pervaporation still not the dominant separation technology?
Click here if you want to know more about the technical value proposition of HybSi® compared to other pervaporation membranes.
What is pervaporation?
Pervaporation is the selective evaporation of one of the components of a liquid mixture using a membrane. The word pervaporation itself is a combination of the words permeation, the transport through a membrane, and evaporation, the phase transition from the liquid to the vapor phase. It is not a pressure driven process such as several filtration processes and reverse osmosis. Instead, the driving force is the chemical potential gradient between feed and permeate side which translates to partial pressure difference, similar to what is found in gas separation membranes. The gradient in chemical potential is maximized by using high feed temperatures and low pressures in the permeate side.
The pervaporation process contains 3 steps:
- Selective sorption on the membrane in the feed side
- Selective transport across the membrane by diffusion
- Desorption in the gas phase under vacuum in the permeate side.
In the figure below the pervaporation process is shown which combines permeation and evaporation.
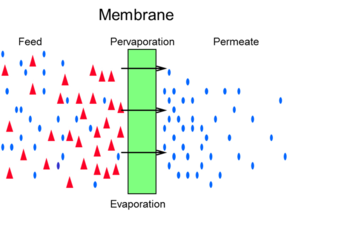
Alternatively to pervaporation, membranes can often be used in vapor permeation mode as well. In this case the feed is fully vaporized. Often a detailed analysis of the full process is required to determine which option offers the highest benefits to the end user. Vapor permeation would be particularly advantageous when the feed stream is already in the vapor phase e.g. a vapor stream leaving a distillation column. Pervaporation and vapor permeation are beneficial for the separation of e.g. azeotropes. In distillation the complete liquid feed is evaporated leading to high energy demands. By replacing distillation by the pervaporation membranes or combining the two processes large energy savings are attainable.
Pervaporation in the waste hierarchy
Using the waste hierarchy to evaluate new processes and technologies yields enhanced environmental protection and financial advantages due to reduced resource and energy consumption, as well as diminished waste disposal requirements. The process of pervaporation, or vapor permeation, is based on the principle of the waste hierarchy by focusing on an integrated approach that prevents and reduces waste while separating molecular mixtures. Accordingly, this is much more sustainable than end-of-pipe solutions that have to be used with distillation separation processes.
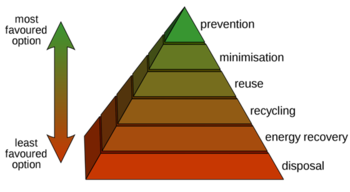
In short, the advantages of pervaporation compared to traditional dehydration or organic separation processes are:
- Prevents the use of entrainers (leading to higher product purity)
- Reduces formation of by-products
- Reduces chemical process steps
- Reduces system dimensions
- Reduces time required for start-up (simply to operate and start-up, start-down)
- Reduces emissions from entrainers, by-products and heat process
These prevention/reduction advantages all result in a significant reduction in energy consumption for the separation process. Moreover, they lead to higher product purity and quality and less resource dependency.
Short-comings of current pervaporation membranes
Despite many advantages of pervaporation and available polymeric and ceramic membranes on the market, pervaporation is still not widely implemented in the chemical industry. This is mainly due to the fact that the currently commercialized polymer and silica and zeolite pervaporation membranes have some shortcomings. The state-of-the art polymer membranes have a limited application window in terms of temperature (up to ~100 °C). Moreover, the polymer membranes have limited resistance against organic solvents and acids. The alternatives, and all ceramic or a zeolite membrane, has a low hydrothermal and acid stability.
Want to learn more about the revolutionary organic-inorganic Hybsi® membrane that tackle all these limitations? Click here.